Screw jacks are devices designed to lift or lower heavy loads, making them a useful addition to machine shops, auto repair facilities, and automotive racing teams.
Your devices can be configured as individual units or multiple devices in series; due to their superior reliability and synchronization, they’re an ideal choice for many applications where traditional methods cannot provide adequate handling solutions.
What is a Screw Jack?
Screw jacks are mechanical motion control devices used to lift, push or pull objects. As highly reliable and synchronized mechanisms, screw jacks play an integral role in automated machinery.
A screw jack converts rotational motion to linear movement through the action of a worm gearbox mechanism. It consists of trapezoidal lifting screws, worm screws, worm gears, and gear housings.
Rotational motion of the worm screw causes its trapezoidal screw to travel linearly in either an upwards or downward direction depending on thread size and ratio of worm gears.
Keyed-for-traveling-nut (KFTN) jacks are designed to offer positive mechanical movement and precise positioning without using a traveling nut with flanges.
These flush mount jacks provide the same level of safety as their more elaborate counterparts while taking up minimal clearance space.
How Does a Screw Jack Work?
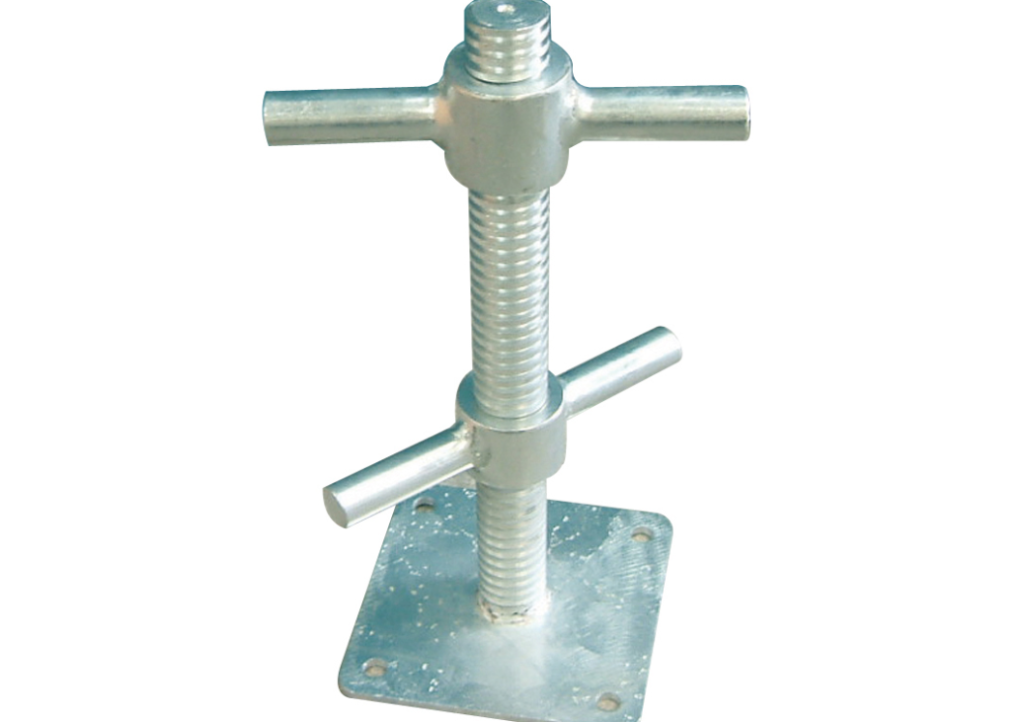
A screw jack is a mechanical device composed of a screw or nut that allows users to raise or lower loads such as cars or machinery.
A jack can be controlled manually or driven by either an AC or DC motor; however, its most popular form of propulsion is typically one general-purpose motor. Jacks are ideal for high-load applications requiring energy efficiency, predictable lifecycles, precision positioning and positional control.
Screw jack designs range from translation (traveling) type to rotating/keyed and bevel gear types, with translating being one of the more popular variations, featuring a lift shaft or screw that moves into or out of a worm gearbox.
What is a Screw Jack Parts?
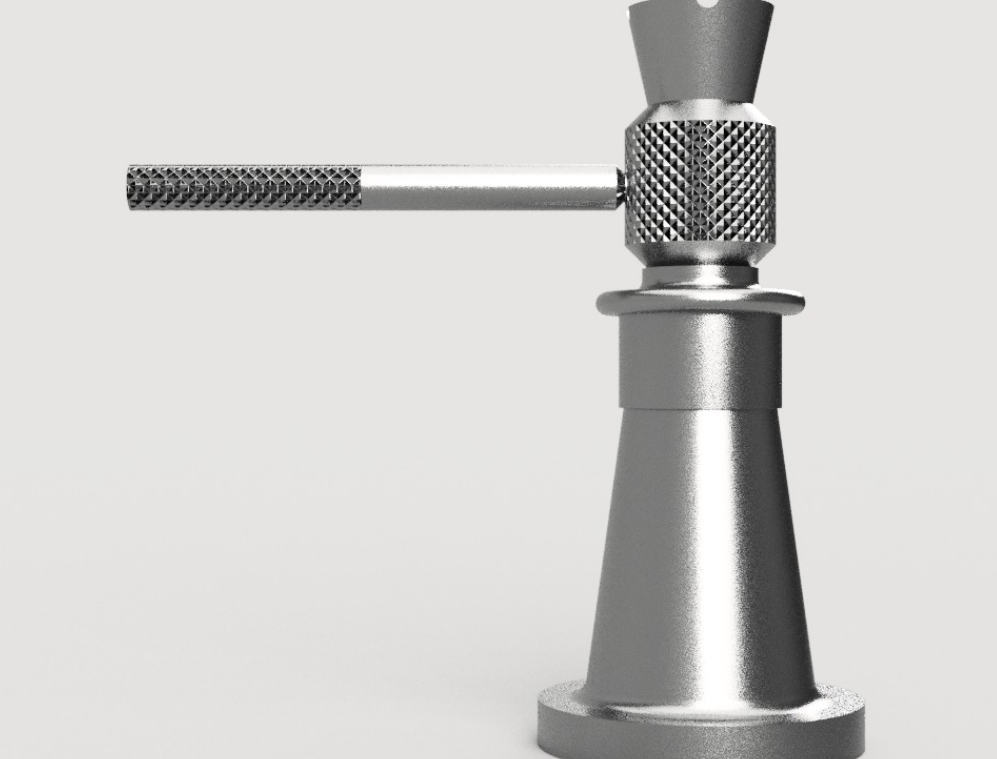
Screw jacks are comprised of a gearbox assembly (with either worm gears or bevel gears) connected to transmission products like lead screws, ball screws or roller screws and motorized through use of a motor, to convert rotary motion into linear movement for lifting and lowering loads from few kilograms up to many tonnes. They can push, pull tension lock unlock tilt pivot roll slide lift & lower loads as much as thousands tonnes.
Hand wheel drive may also be an appropriate power source depending on the application. Screw jacks have numerous industrial applications, from single unit lifts of several tonnes up to multi-tonne lifts with linked units lifting in unison, all the while keeping their load steady and level. For enhanced reliability the best screw jacks include self-locking features in case of power loss and high overload capacities to address side loading stress; they may even feature high carbon steel or bronze components and feature heatproof construction to withstand anode smelting at aluminium plants as well as handle abrasive alumina dust emissions from anode smelting operations – perfect for anode Smelting plants where anode Smelting takes place!
What is a Screw Jack System?
Screw Jack Systems provide all the components required for pushing, pulling, lifting and positioning loads in motion – including bevel gearboxes, motors, couplings, plummer blocks and motion control devices.
Screw jacks come in various varieties to meet any application need – from trapezoidal screw thread types to ball screw models.
When selecting a jack for your application, it is essential that you consider which design best meets its purpose. For instance, do you require translating or keyed for non-rotation (TKN) jacks; keyed for traveling nut (KFTN) models may also work?
Translation screw jacks typically sit under loads and require a recess for their screw to retract into, while keyed for travelling nut jacks often mount flush to solid surfaces with their free end requiring a flange bearing for smooth operation and an aesthetically pleasing appearance.